Fab Masters Offers Prototyping and Design Assistance
Utilizing a specialist in fabricating extruded aluminum can be invaluable in product development. In early 2011, Fab Masters Company, Inc. was approached by SAPA Group to be involved in a prototyping team to help manufacture a new utility vehicle, the CV-23. Throughout the past year, Fab Masters assisted with prototyping and fabricating a number of aluminum frame assemblies for UPS’s new utility vehicle.
This project presented Fab Masters 100 different part numbers, many were frame assemblies. The components for the first 150 vehicles were machined, while punch tooling was being developed for more cost-effective fabrication processing. Substituting composite plastic panels for the aluminum, and aluminum for steel framing would lower the truck’s fuel consumption by 40 percent, in comparison to the old P70.
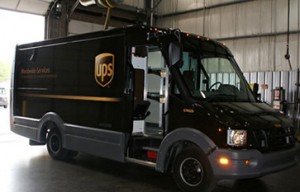
Sam Cropsey, Fab Masters’ Sales Manager, said, “The biggest challenge of this project was getting complete collaboration with the supply chain, so we could help them reduce cost.”
There were difficulties at the onset because so many people were involved, but after a core committee was installed making communications clearer and easier, straightforward progress proceeded.
The second phase of cost reduction is about to take place. An example is the transformation of a sheet metal part into an extrusion. A cross-framing part that was formed sheet aluminum is being redesigned into an extrusion, saving 100% of the forming process, and $.50/lb on sheet material. This part cost $7 when made from sheet metal as opposed to $4 when made from extrusion.
UPS Putting 150 Plastic-Body & Aluminum-Frame Trucks into Service
Lightweighting using aluminum in automotive is increasing in popularity, as it has been shown to reduce fuel consumption without sacrificing performance or safety. UPS estimated that these trucks would decrease fuel expenditure by 40 percent.