We recently purchased a granite surface plate, and whenever guests see it or it is mentioned in conversation the response is the same, “Wow you’ve got a 10-foot granite table”! Well, the “big deal” is – If you are a manufacturer of precision parts and assemblies, especially where parts will need to be connected to a surface area in an air-tight or liquid-tight manner, flatness is a critical quality of the manufactured surfaces.
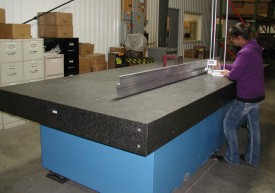
A granite table lets you see if your parts are indeed flat or if they are warped or twisted. In a case where two pieces have been joined, it allows you to see if the completed piece is true and flat. By placing the part on this flat surface you can see if twist or bow is present, and measure the defect accurately. This is especially visible in a long piece of extruded material or if two pieces were joined together improperly.
A granite surface plate is a true flat surface. It is made that way by grinding two pieces of granite together until they are absolutely flat. Two parts that are flat can be “wrung” together, which means they will cling to each other when placed in contact. This phenomenon is called wringing, which causes their ultra-flat surfaces to cling together, and is commonly used with gage blocks.
This specific granite table is uncommon in this size, most being one-third this size or smaller. It helps us a great deal with the inspections of large-scale parts. We are fortunate enough to have a large building so we have been able to strategically place this table in close proximity to our new line of CNC routers. These routers are primarily dedicated to larger parts that we could not fit inside our quality lab, let alone on our smaller tables. In addition to using the table for larger parts, we have also found significantly increased efficiency when sorting parts. When a quality issue arises we are able to place questionable smaller parts simultaneously on the table allowing a very rapid inspection and efficient process.